Press-in technique
The QMP Series
The QMP series press-in units are designed for both compression and tension forces and stand out with their compact construction in a slim square stainless steel housing – ideal for confined spaces and modular system concepts.
The digital force sensor is integrated directly into the plunger and protected against overload. Stroke measurement is performed via a high-resolution absolute stroke measurement system.
LED status indicators on the unit provide immediate feedback on operating status and process results.
With various stroke lengths and optional features, the QMP series offers a high level of adaptability – for both simple and demanding press-in applications.
In combination with the MultiPro 3G control system, precise force transducers and exact position measurement ensure consistent, repeatable results – with complete process documentation.
Technical Features at a Glance:
-
Maintenance-free, brushless servo motor – for maximum service life
-
Robust square stainless steel housing
-
Optional: Space-saving design with motor offset
-
Precise force and stroke measurement via calibrated force sensor and absolute stroke measurement system
-
No reference run required thanks to absolute measurement
-
Designed for both compression and tension forces – with high repeatability
-
Immune to electromagnetic interference thanks to digital data transmission
-
Optional: Force retention via electromechanical holding brake (HB), backstop (RS) with force control, or motor holding brake (MHB – individually or in combination with RS)
-
Optional sealing air connection and cooling fan for protection during continuous operation
QMP 80 Series

Press-in unit with brushless, electronically controlled servo motor, digital force sensor, absolute stroke measurement system and status display.
The QMP-80 series is available in a basic design with a stroke of 200 mm, 300 mm or 500 mm. Nominal forces of 2.5 kN, 5 kN, 10 kN, and 20 kN are available – in DR version (compression) or DZ version (compression and tension).
Features
- Servo motor, motor attachment vertical
- Force sensor direct-acting, installed in the plunger
- Precision of force measurement 0.5% of the final value
- Displacement sensor (absolute encoder) directly fitted on the ball screws
- Distance repeat precision 0.01 mm at approx. 20 mm/s
- Distance measurement resolution 0.003 mm
- Light field for displaying press-in status
- Stamping speed max. 200 mm/s in both directions continuously variable
Force Ranges
- QMP 80 / 025: 0.4 to 2,5 kN
- QMP 80 / 05: 0.8 to 5 kN
- QMP 80 / 10: 2 to 10 kN
- QMP 80 / 20: 4 to 20 kN
Standard options
- Motor offset (the motor is laterally offset by 180°) for optimisation of the size.
- Motor holding brake for higher tool weight as well as in combination with backstop for braking the movement.
- Holding brake — blocks the drive moving in and out (holding time max. 999 s), i.e. to move the plunger of the press-in unit, the brake must be switched off.
- Backstop — blocks the drive only when moving in (holding time as long as desired). Due to the mechanical design (free-wheel, almost backlash-free), the plunger is inhibited against “pushing in” in any position and can thus hold a counterforce. The permanent holding of the set force is guaranteed by the regulation by means of the stepper motor control.
Accessories
- Fan unit for cooling the motor
- Sealing air connection — avoids the ingress of dirt particles into the press-in unit
- Portal frame manufactured according to customer-specific requirements
- C‑frame manufactured according to customer-specific requirements
- Service package — lubrication set
Weights
- With 200 mm stroke: approx. 21 kg
- With 300 mm stroke: approx. 25 kg
- With 500 mm stroke: approx. 35 kg

QMP 100 Series

Press-in unit with brushless, electronically controlled servo motor, digital force sensor, absolute stroke measurement system and status display.
The QMP-100 series is available in a basic design with a stroke of 200 mm, 300 mm or 500 mm. Nominal forces of 30 kN, 40 kN, 50 kN, and 60 kN are available – in DR version (compression) or DZ version (compression and tension).
Features
- Servo motor, motor attachment vertical
- Force sensor direct-acting, installed in the plunger
- Precision of force measurement 0.5% of the final value
- Displacement sensor (absolute encoder) directly fitted on the ball screws
- Distance repeat precision 0.01 mm at approx. 20 mm/s
- Distance measurement resolution 0.003 mm
- Light field for displaying process status
- Stamping speed max. 200 mm/s in both directions continuously variable
Force Ranges
- QMP 100 / 30: 6 to 30 kN
- QMP 100 / 40: 8 to 40 kN
- QMP 100 / 50: 10 to 50 kN
- QMP 100 / 60: 12 to 60 kN
Standard options
- Motor offset (the motor is laterally offset by 180°) for optimisation of the size.
- Motor holding brake for higher tool weight as well as in combination with backstop for braking the movement.
- Holding brake – blocks the drive moving in and out (holding time max. 999 s), i.e. to move the plunger of the press-in unit, the brake must be switched off.
- Backstop – blocks the drive only when moving in (holding time as long as desired). Due to the mechanical design (free-wheel, almost backlash-free), the plunger is inhibited against “pushing in” in any position and can thus hold a counterforce. The permanent holding of the set force is guaranteed by the regulation by means of the stepper motor control.
Accessories
- Fan unit for cooling the motor
- Sealing air connection – avoids the ingress of dirt particles into the press-in unit
- Portal frame manufactured according to customer-specific requirements
- C‑frame manufactured according to customer-specific requirements
- Service package – lubrication set
Weights
- With 200 mm stroke: approx. 45 kg
- With 300 mm stroke: approx. 50 kg
- With 500 mm stroke: approx. 60 kg

QMP 140 Series
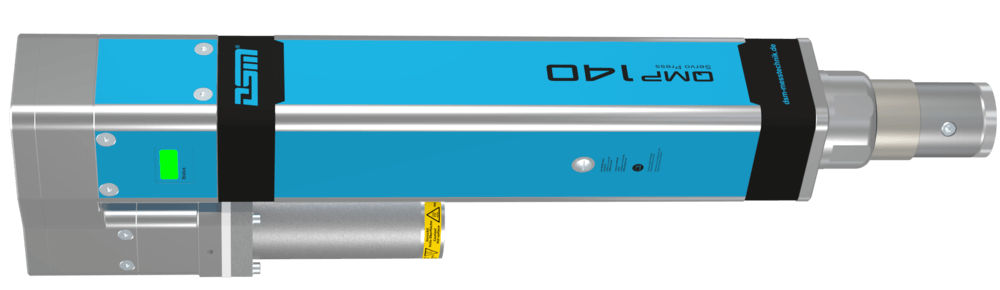
Press-in unit with brushless, electronically controlled servo motor, digital force sensor, absolute stroke measurement system and status display.
The QMP-140 series is available in a basic design with a stroke of 200 mm, 300 mm or 500 mm. Nominal forces of 70 kN, 100 kN, and 120 kN are available – in DR version (compression) or DZ version (compression and tension).
Features
- Servo motor, motor attachment angled via motor offset
- Force sensor direct-acting, installed in the plunger
- Precision of force measurement 0.5% of the final value
- Displacement sensor (absolute encoder) directly fitted on the ball screws
- Distance repeat precision 0.01 mm at approx. 20 mm/s
- Distance measurement resolution 0.003 mm
- Light field for displaying process status
- Stamping speed max. 100 mm/s in both directions continuously variable
Force Ranges
- QMP 140 / 70: 10 to 70 kN
- QMP 140 / 100: 20 to 100 kN
- QMP 140 / 120: 24 to 120 kN
Standard options
- Motor holding brake for higher tool weight as well as in combination with backstop for braking the movement.
- Holding brake – blocks the drive moving in and out (holding time max. 999 s), i.e. to move the plunger of the press-in unit, the brake must be switched off.
- Backstop – blocks the drive only when moving in (holding time as long as desired). Due to the mechanical design (free-wheel, almost backlash-free), the plunger is inhibited against “pushing in” in any position and can thus hold a counterforce. The permanent holding of the set force is guaranteed by the regulation by means of the stepper motor control.
Accessories
- Fan unit for cooling the motor
- Sealing air connection – avoids the ingress of dirt particles into the press-in unit
- Portal frame manufactured according to customer-specific requirements
- C‑frame manufactured according to customer-specific requirements
- Service package – lubrication set
Weights
- With 200 mm stroke: approx. 100 kg
- With 300 mm stroke: approx. 175 kg
- With 500 mm stroke: approx. 215 kg
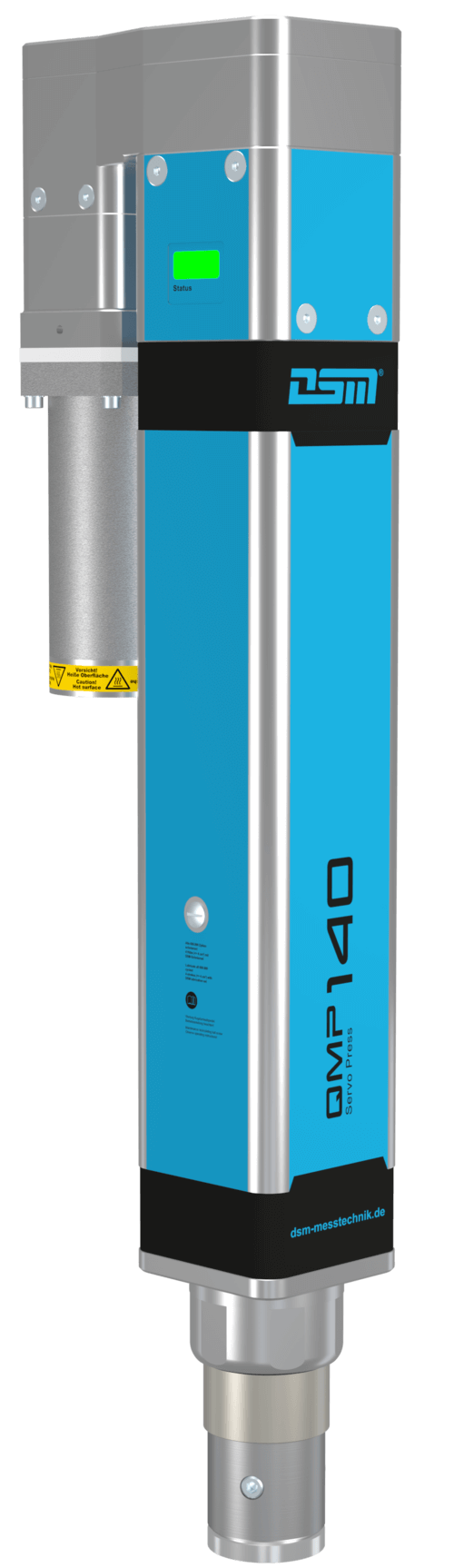